Introduction
Potential EV shoppers will sometimes hear the subject of battery thermal management come up. Some EVs have a liquid cooled battery. Others have an air cooled battery, while some have no cooling whatsoever. What is the difference? And why is it important? And why have some highly reputable automakers with decades of experience opted for such completely different approaches?
In this article, we’ll cover why batteries generate heat in the first place and why they don’t like the cold either. We’ll cover some of the science of battery heat and why excess heat is best avoided. As with all engineering decisions, the final product is a compromise of competing goals, be they size, weight, cost and safety. If you’re in the market for an EV, the long-term impact of thermal management could be a deal breaker.
Chemistry and Ohm’s law
All battery packs generate heat when being charged or discharged. The lithium ion cell consists of two composite electrode structures; the cathode and the anode, separated by a porous polyethylene. Lithium ions are intercalated, or ‘sponged’ into the anode structure when the battery is charged (Fig. 1). Concurrently, Li+ ions are evicted from the cathode’s crystal structure. The anode and cathode are separated by a porous polyethylene membrane which prevents them from touching, but allows Li+ ions dissolved in organic electrolyte to move. During discharge, the current is reversed and the Li+ ions move back into the cathode. Cathodes are usually made from a combination of lithium metal oxides bound to the aluminium foil with carbon and other polymers. Most Li-ion battery cells use a graphite-based anode on a copper collector. Graphite is electrically conductive, so it can easily conduct the flow of electrons through to the copper collector.
The charging of a Li-ion cell is analogous to a multi-story carpark, where Li+ ions are cars. From empty, the carpark fills rapidly as all cars find a parking spot with ease. However as the carpark fills, it gets harder and harder to find a vacant spot, so the flow of ions decreases (resistance increases). Forcing more cars to enter the parking lot will only cause damage and generate heat.
Whenever current is flowing, the total internal resistance of the cell will determine how much heat is generated. The rate of heat generated by the cell during charge or discharge is proportional the internal resistance multiplied by the current squared:
P = I2 x R
Where power P is in watts, current I is in amps, and resistance R is in Ohms. It is this equation which drives almost all of the heat generated in a battery during charge or discharge.
The Li+ ion rich electrolyte serves as the internal conductor in the circuit. The mobility of these ions determines part of the cell’s own direct current internal resistance, or DCIR. The aluminium and copper collectors themselves are crucial too – the thicker the foil, the more current it can carry. Finally, the particle size and thickness of the anode and cathode matrix also drives the impedance of the cell – conductive materials like graphite and graphene is used to conduct electrons and lower the DCIR.
Figure 1. Basic representation of a Li-ion electrochemical cell. From: Understanding electrochemical potentials of cathode materials in rechargeable batteries, Materials Today, 19(2):109-123
Arrhenius Equation (the main reason you need thermal management)
Swedish chemist Svante Arrhenius (1859-1927) is known for many things, including some of the earliest work on carbon dioxide’s role in global warming. However, he is best known for describing the relationship between the rate of chemical reactions and the temperature at which they occur – put simply, it is that the warmer it is, the faster the reaction.
Temperature is best described as the average kinetic energy of the particles which make up substance; at the molecular level, everything is vibrating and bumping into each other. Chemistry is what happens when molecules bump into each other and either loose or gain electrons; so the more energy you add to a system, the faster they bump into each other and the quicker the reaction happens. Temperature has an exponential effect on reaction rates; increasing the temperature by 10°C approximately doubles the reaction rate.
Li-ion battery packs work better when they are warm. Most EV drivers will know their range may increase by as much as 10 % during summer. This is because the internal resistance of the cell is reduced due to improved ionic mobility. Low ionic mobility is the main reason you shouldn’t charge a lithium battery quickly in low temperatures; the ions tend to accumulate and plate onto the anode, decreasing the inventory of lithium and ultimately decreasing the capacity of the pack. So batteries have a “goldilocks” zone around 25°C. However, good chemistry isn’t the only thing that takes place faster at higher temperatures – bad chemistry, the kind which blocks up the spaces for ions, degrades electrolytes and accelerates the breakdown of active material, all happen faster at higher temperatures too (Fig 2). In fact if the temperature gets high enough, the cathode material itself can start to decompose, leading to thermal runaway. This is why thermal management is critical – the cells must not get too hot or too cold, under normal operation.
Figure 2. A long list of all the things that ruin your battery. Temperature gets plenty of mentions. From: Degradation diagnostics for lithium ion cells, Journal of Power Sources 341 (2017) 373-386.
Specific heat capacity
When something absorbs heat, its temperature rises. The specific heat capacity is an intrinsic property of all materials, with water sitting at the top of the list. A kilogram of water can absorb an incredible 4.2 kJ of heat, raising its temperature by just 1°C. A li-on battery pack has a heat capacity about half that of water, so it’s temperature rises more quickly for the same amount of heat energy. If a liquid coolant is used for the battery, the higher the heat capacity the better. However water near a battery pack is also a massive corrosion risk. Non-aqueous coolants like Novec™ or paraffin have advantages in that salts are completely insoluble in them. This means they are effectively corrosion-proof liquids. However the downside is their significantly lower specific heat capacity; at almost half that of water, they will only absorb half as much heat for the same temperature rise.
Moving heat – Conduction, convection and radiation
Excess heat will lead to higher battery temperatures and in extreme cases, cause a fire. So keeping the battery cool, or at least under 35°C is the goal. So how do we achieve this? Heat is driven from the source by three means – conduction, convection and radiation.
Conduction is the process where heat is transferred through a uniform, usually solid material. Different materials are better conductors of heat than others. Metals like silver, copper and aluminium are among the most thermally conductive materials around, but they are also great conductors of electricity. The risk of a short circuit is enormous, so insulating materials with reasonable thermal conductivities like silicones and filled epoxies are often used between battery cells and the metallic cooling surfaces. Again, a difficult compromise has to be made here – the interfacing material needs to be thermally conductive, electrically isolating, light weight and not take up too much space. These are not easy properties to reconcile, so its little wonder materials scientists are working on better fillers and adhesives for this role.
Related to conduction, convection is when the air on the boundary layer of a hot source absorbs heat and rises. Cooler air continuously takes its place, resulting in a net heat transfer to the surroundings. Air is not a very good thermal conductor, but it’s markedly better than a vacuum.
Finally, radiation is when a body at a high temperature loses energy through space in the form of long wave infrared radiation. This is why a hot metal ball will still lose heat to its surroundings even in a vacuum. Radiative loss in an EV battery is a minor component, but it occurs nonetheless.
In all cases the process is the same – a large difference in temperature drives heat transfer (Fig. 3). Better conductors will allow more heat to be moved with lower temperature differences, and this heat may be dumped into a medium which has a high specific heat capacity away from the source. So with this in mind, how would one cool a hot battery without compromising its integrity?
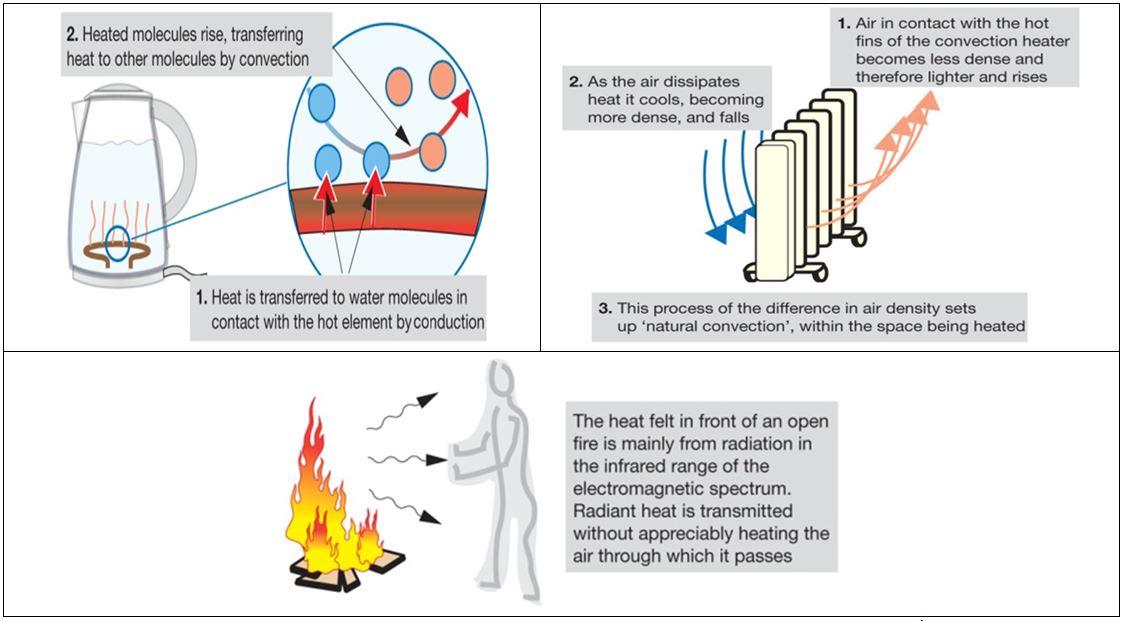
Figure 3. Conduction, convection and radiation. Source: Pethebridge &Neeson - Electrical Wiring Practice, 7th ed.
Battery thermal management approaches
As EV batteries get bigger and more energy dense, the cells used in the battery will have internal resistances, meaning they will generate more heat when discharged and charged. That heat needs to be regulated to prevent the pack temperature from exceeding 35°C. Let’s look at three commonly deployed approaches:
Liquid heat exchange (Tesla, Hyundai, Chevy)
Liquid heat exchange systems are currently the most common approach in automotive battery thermal management. This involves using a thermally conductive, yet electrically insulating union between the heat source (the battery cells) and the sink (the liquid coolant) as well as somewhere to dump this heat, like a liquid-air radiator or liquid-refrigerant heat exchanger. If the coolant is hotter than ambient air, it can simply shed this heat via a radiator. However, as this process relies on a large temperature difference, it is pretty much ineffective in hot climates. More commonly, the coolant is passed through a liquid-refrigerant heat exchanger, which is supplied by the vehicle’s air conditioning system (Fig. 4). Refrigerant is expanded into a multi-plate heat exchanger. As it vaporises, it absorbs latent heat, lowering the temperature to just above freezing. This large temperature difference drives the heat transfer more effectively, lowering the temperature of the coolant, and further reducing the temperature of the battery. The heat is ultimately lost via the A/C condenser, which typically operates at about 80°C.
Figure 4. The Hyundai Kona EV has a liquid cooled (and heated) battery. Heat is absorbed by the water-based coolant (thick green hoses) and exchanged with air conditioning refrigerant. Image: Hyundai.
Liquid heat exchange systems are generally more complex and add cost to manufacture. Critically, they are prone to coolant leaks which might result in catastrophic consequences. The most important feature of the liquid cooled battery is the union of thermally conductive surfaces as close as practical to the cells as practical, without compromising electrical insulation or cooling circuit integrity (Fig. 5). It is this element of battery pack design which causes the most grief for automotive manufacturers; how to maintain a high level of thermal conductivity between cell and cooling medium, while at the same time ensuring the battery is completely electrically isolated. Several product recalls and service bulletins relating specifically to coolant leakage and subsequent corrosion of battery components have been reported for several makes of EV.
Figure 5. The Tesla Model 3 has liquid cooling channels glued to the cells with a thermally conductive, electrically insulating adhesive (dark grey) as well as a space-filling encapsulant (blue). Great care has gone into ensuring electrical isolation is maintained throughout the battery pack. Image courtesy of Munroe Associates.
Chilled air exchange (Renault, Lexus, Mitsubishi)
Chilled air exchange systems pass refrigerated air through the battery pack, cooling it by convective means. Air can be a very effective heat transfer medium, despite having significantly lower thermal conductivity and specific heat capacity: it’s light, it’s free, and it’s electrically non-conductive. Some manufacturers pull cool cabin air through the battery pack and expel it to the outside, while others like Renault and Lexus recirculate the same air via an A/C evaporator. The main drawback to air cooling is the non-uniformity of heat removal. If the flow of air around a complex battery structure is higher or lower in places, the battery will develop hot spots. These highly localised differences in temperature will drive accelerated degradation of the battery, so great efforts are made to ensure the flow throughout the pack is as consistent as possible.
Convection cooling only (Nissan)
In its simplest form, a sealed battery pack will lose heat to its surroundings through convection alone. There may be many layers of structure between the cells of the battery and the outside air, all of which slow the transfer of heat. In cooler climates this approach is entirely reasonable, as it would take a significant duty cycle to generate enough heat to exceed 35°C. However in a hot climate, the difference in temperature between inside and out might be so small, or indeed negative, that the battery actually gains heat from the surroundings.
Figure 6. The Nissan Leaf battery has no internal cooling system – it simply loses heat to the surroundings by convection. Image: Nissan.
A passively cooled battery pack has several advantages over the alternatives – they are substantially cheaper, they cannot leak and they are fast to assemble. It does rely on the battery chemistry being robust enough to handle temperature extremes, and Nissan has gone to some lengths to ensure the cells are able to tolerate warmer conditions (Fig. 6). The obvious disadvantage is the risk of overheating the battery, particularly in heavy duty cycles such as repeated fast-charging on a summer road trip. The battery management system may enforce charge and discharge limits, reducing power to minimise temperature rise.
So what should I look for in an EV?
The first thing to consider is how you intend on using the vehicle. If you primarily use it to commute to work and long hot road trips are infrequent, you might be able to get away with a passively cooled battery. This would be particularly relevant to those who live in cool climates. However if you live in a hot climate, and long road trips with regular rapid charges will be commonplace, then a more sophisticated cooling system is needed. You can still go without, but the risk of premature battery degradation is significant.
Electric vehicles with complicated cooling loops, bypass valves, A/C expansion valves and motor heat recycling systems are a fine example of innovation in heat management, but they also add complexity to the vehicle, providing plenty of opportunities for things to go wrong.
As always, high states of charge for long periods of time are also factors for battery degradation and high temperatures will simply speed this up further.